L3455 Professional Sheet Metal Fabrication Book 304 Colour Pages This Book Is For People Who Love Ol

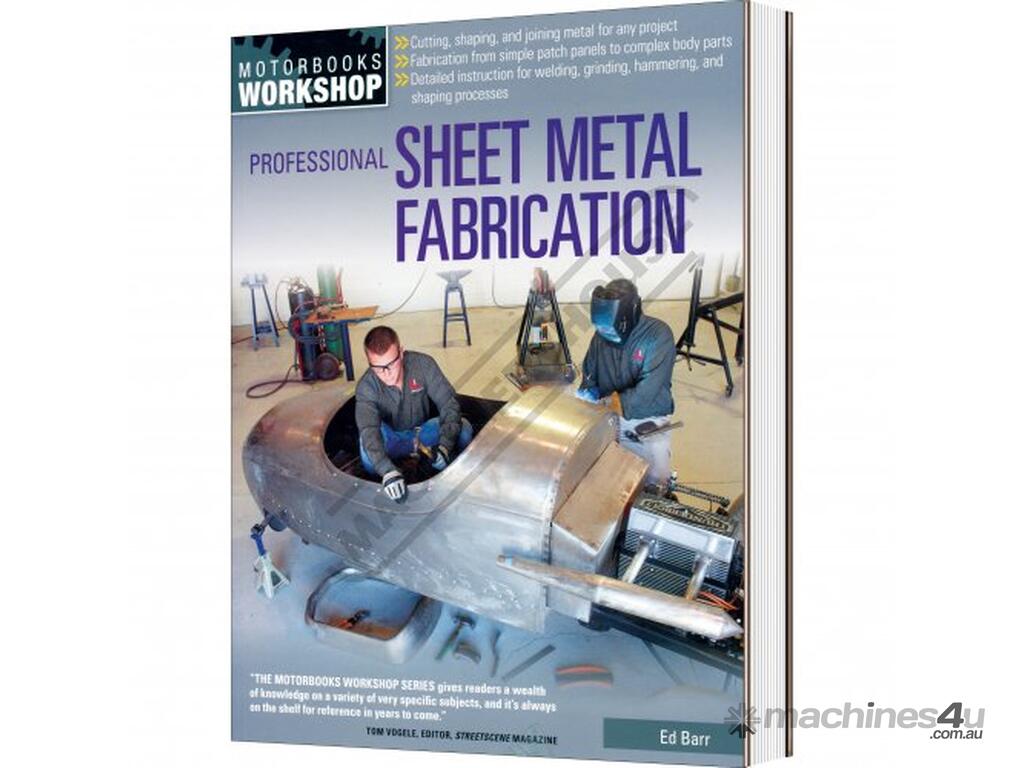
L3455 Professional Sheet Metal Fabrication Book 304 Colour Pages This Book Is For People Who Love Ol : $50 AUD ($55 Inc. GST)
HAFCO L3455 Professional Sheet Metal Fabrication Book 304 Colour Pages This Book Is For People Who Love Old Cars & Who Want To Make/Repair Their Old Car's Sheet Metal with Their Own Hands
CALL NOW AND DO A DEAL! ADD THIS ASSET TO YOUR WORKSHOP
WE OFFER MACHINERY SOLUTIONS AT AFFORDABLE PRICES.
Order Code: L3455
This book is for people who love old cars and who want to make their old car's sheet metal better than new with their two hands. The practice of restoring antique cars is a complex, time-consuming , yet incredibly rewarding experience. It taxes your patience and financial resources, but for some of us it is as essential as oxygen. As with all the different facets of auto restoration-soft trim, paint, mechanical work, and more sheet metal repair provides the opportunity to transform the quality of something from extremely bad to extremely good or at least in much better condition than it was. Sheet metal fabrication allows you to make something beautiful out of thin air. Whether you are patching a small rust hole or making an entire fender, at the end of the day (or at least at the end of most days) you will feel good about having made tangible, measurable progress.
For people with little experience in shaping metal, the idea of making panels or parts of panels from scratch is more than a little daunting. Shaping sheet metal is intimidating only because the logic behind it isn't immediately apparent. Most car enthusiasts understand how a flywheel turns because it is attached to a crankshaft, which turns because pistons push on it in a certain way, and so forth. Sheet metal seems to have a mind of its own, however-you hit it in one spot and it moves as expected , but another part of it may bend or change shape as well. Fortunately, working with sheet metal is neither black magic nor rocket science (though certainly some knowledge of science is important). If you were to ask a group of experienced metal shapers what it takes to succeed in their field, I'm sure it would come down to thoughtful persistence and a knowledge of materials; if at first you don't succeed, take a different approach and try again. Sometimes making something out of sheet metal will take much, much longer than you anticipate, but in my experience effort always pays off in this discipline.
In this book I present a number of techniques for making and repairing automotive sheet metal components. As your skills increase, think of ways to solve progressively difficult problems by combining multiple processes. Many projects seem impossible to carry out unless you break them down into smaller tasks that involve one or more techniques. Furthermore, don't be afraid to make mistakes; making one or more false starts is still progress-you've learned a couple of ways not to do something. When talking to students, I call false starts the research and development phase. The organisation of this book resembles the sequence I prefer to follow when introducing new students to sheet metal restoration. I begin with joining and cutting processes because they are absolutely essential to making automotive related objects out of sheet metal, and acquiring welding skill takes time. Starting with welding means that you'll have more of your life ahead of you to practice. I introduce metal shaping processes next and conclude with a series of hands-on projects intended to illustrate common automotive sheet metal problems and how to solve them. Now let's get to work.
CHAPTER 01 - GETTING STARTED
- Safety & fashion sense
- Make a plan
- Getting Organised
- Tool - hammers & dollies
- Spoons & slappers
- Corking & driving tools
- Prying tools
- Miscellaneous tools
- Bead roller
- English wheel
- Slip roll
- How to make a shot bag
CHAPTER 02 - SPECIAL TECHNIQUES FOR WELDING SHEET METAL
- Oxyacetylene or gas welding
- Setting up your equipment
- Lighting & adjusting the torch
- Shutting down the torch
- How to weld
- A flange weld with filler rod
- Butt joints
- Torch welding aluminium
- Mig welding (Metal inert gas welding)
- Tig welding
- Tungsten electrodes
- Tig welding aluminium
- Tig welding stainless steel
CHAPTER 03 - BRAZING, SOLDERING & RIVETING
- Brazing & soldering
- Old fashion lead body soldering
- Some things to avoid when leading
- Lead sleds
- Lead free solder
- Riveting
CHAPTER 04 - CUTTING SHEET METAL WITH THE OXYACETYLENE TORCH & PLASMA CUTTER
- Oxyacetylene cutting torch
- Using the torch
- Plasma cutting
CHAPTER 05 - BEGINNING SHEET METAL SHAPING
- Stretching & shrinking metal
- Simple mechanical shrinker stretchers
- Hammer forms
- Stumps
- English wheels
- Beading
- Copying shapes
CHAPTER 06 - THE SMALL GAS TANK PROJECT
- Marking out
- Hammering the flange ends
- Beading the ends
- Using the slip roll
- Hammering the ends
CHAPTER 07 - ADVANCED SHEET METAL SHAPING
- Power hammers
- Shrinking the pieces
- Stretching the pieces
- Beading
- Planishing Hammers
- Advanced demonstration "Ford grille shell"
- Wire buck building
- Styrofoam & wood bucks
CHAPTER 08 - BUILDING A FENDER FROM CONCEPT TO COMPLETION
- Early concept & construction
- Finishing the first fender section
- Welding the fender
- Finish sanding the fender
CHAPTER 09 - MAKING IT BEAUTIFUL: STRAIGHTENING, GRINDING, & SURFACE FINISHING
- Removing paint & oxidation
- Metal straightening
- Troubleshooting
- Heat shrinking
- Shrinking with resistance welders, stud guns & shrinking discs
- Straightening a door
- The shrinking disc
- Welding grinding & surface finishing
- Buffing & polishing
- Electroplating
CHAPTER 10 - BUILDING A CUSTOM PEDAL CAR
- Initial plans & welds
- Fabricating the exhaust system
- Fabricating the wheel arches
CHAPTER 11 - FLOOR-PANS, ROCKER PANELS, & REAR QUARTER PANELS
- Floor-pans
- Rocker panels
- Quarter panel repairs
- Ford model A rear quarter panel repair
- Mustang wheel arch
CHAPTER 12 - REPAIRING DOORS
- Door skins
- Cutting the door steel
- Cut the door
- Lay the skin
- Trouble shooting door gaps
CHAPTER 13 - REPAIRING FENDERS, HOODS & TRUCK LIDS
- Fender fun
- '57 Chevy fender repair
- Modal A fender repair
- Hoods & trucks
Specifications:
ORDER CODE: L3455
Title: Professional Sheet
Title: Metal Fabrication Book
Number of pages (No.): 304
To Purchase Online Please Visit The Machineryhouse Website & Search For 'L3455'
Visit us in-store at:
Sydney - Unit 1, 2 Windsor Road, Northmead NSW 2152
Melbourne - 4 Abbotts Road, Dandenong South VIC 3175
Brisbane - 625 Boundary Rd, Coopers Plains QLD 4108
Perth - 11 Valentine Street, Kewdale WA 6105